Vibratory driving
Vibratory driving is one of the most important methods used in specialized civil engineering. It is based on the principle of turning the soil into a quasi-liquid state by vibrating the pile section. The vibrations reduce the skin friction of the pile section and allow rapid driving progress. Vibrators can be leader-guided, free-riding or mounted on an excavator.
Reliable performance even in the toughest projects: müller vibrators.
müller vibrators have a proven track record in foundation engineering stretching back 60 years. Suitable for a wide range of applications, their reliability and constant development make them a crucial part of day-to-day practice.
There is specially tailored equipment for every application: systems on a pile driver ram are exceptionally powerful and ideal for large and complex construction sites. Excavator-mounted vibrators are designed for use in urban settings. Leader-guided units are impressively easy to transport and quick to set up on site.
Vibrators and power packs are part of the conventional setup of a modern system. The power pack – driven by a diesel motor – delivers the oil flow for the vibrator through hydraulic pumps, ensuring that the vibrator is supplied with energy to drive steel sheet piling into the ground using vibration.
müller vibrators H series. With fixed eccentric moment.
müller vibrators with constant amplitude – straightforward to use and robust. That is the foundation for good results in moderately difficult driving conditions. These vibrators are fitted with eccentrics that generate a fixed eccentric moment. With force-feed lubrication and oil cooling, this series is equipped for applications in extreme climatic conditions.
Applications
Soils with light to moderately difficult driving conditions
Driving and extracting tubular piles
Also in extreme climatic conditions
MÜLLER vibrators HHF series. Two in one.
These incrementally adjustable vibrators are ideal for use in changeable geological conditions. The eccentric moment can be increased through removable additional weights, so with one machine, different amplitudes and frequencies adapted to the soil profiles can be achieved with the same centrifugal force.
Applications
- Soils with moderate to difficult driving conditions
- Suitable for heavy piles
müller vibrators HFV series. Variable and resonance-free.
These vibrators offer maximum performance with minimum ground vibration – ideal for applications in urban foundation works or in areas sensitive to vibration, all thanks to resonance-free starting and stopping. In addition, the amplitude can be infinitely varied during operations. The natural frequency of the soil can therefore be taken into account – driving proceeds effectively and yet with little vibration.
Applications
- Urban foundations works
- Areas sensitive to vibration
- Ideal for sandy soils
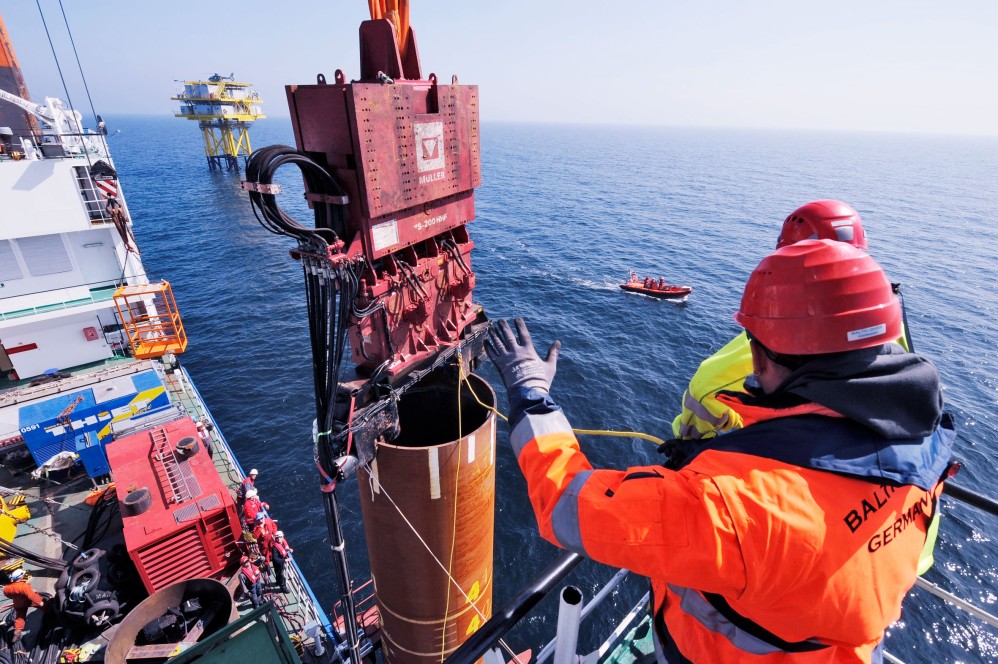
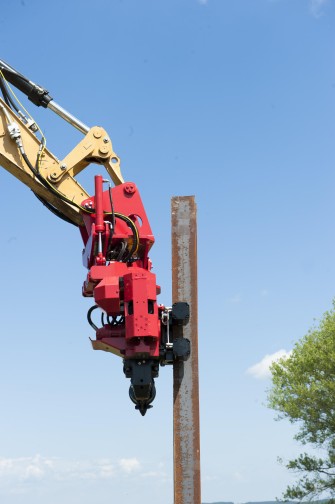
Excavator-mounted vibrators. Compact all-rounders.
The compact, lightweight müller excavator-mounted vibrators can be attached to any
standard excavator. The power comes from the on-board hydraulics and the units are
controlled by the excavator’s control levers. Various models (HFB, HFBV, HFBS, HFB SG) and useful accessories are available to suit even the most diverse applications.
Applications
Driving and extracting (MS-2 to MS-9 HFB)
Suitable for sheet piling and tubular piles with a modified clamp arrangement (MS-4, MS-6, MS-7, and MS-9 HFB)
Installation of plastic and timber piles, lightweight sections, and reinforcing cages (MS-1 HFB)
For urban areas sensitive to vibration (MS-5 HFBV, MS-7 HFBV, MS-8 HFBV, MS-10 HFBV)
Suitable for heavy soils (MS-9 HFB, MS-17 HFB)
Piles can be picked up and set down directly with the clamp (MS-4 to MS-7 HFBS)
Advantages
Small and compact Easy operation with a safety circuit Quiet and universal in application Extremely low height allows driving of long piles High push/pull forces increase driving performance All clamps can be rotated through 90° to allow face working Easy to attach Option: double clamping devices can be fitted for driving tubular piles Option: can be fittet with cooling system Option: can be modified for operation with power pack
Leader-mounted vibratory hammers. For tight spaces.
müller leader-mounted vibratory hammers are the specialists for tight corners. They are mounted on leaders and offer contractors an adjustable moment plus resonance-free starting and stopping.
Applications
Driving and extracting sheet piles, tubular piles and H sections Foundation methods such as compacted gravel or sand columns
Driving and extracting single sheet piles with small dimensions
Compact design
Driving and extracting on cramped sites
Resonance-free starting and stopping
Minimum vibrations and emissions
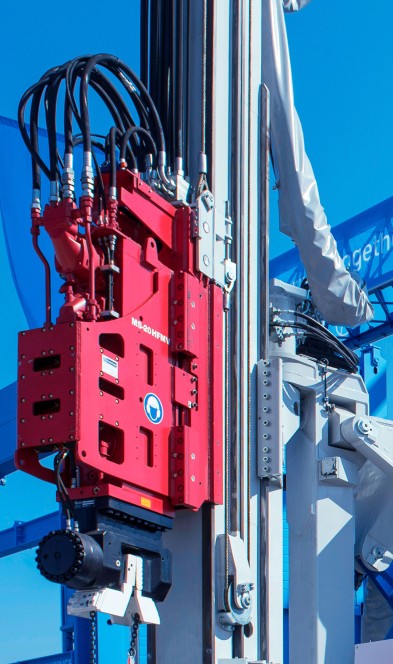
Drill drives. Rounding off the range.
These robust, low-noise drilling units are quickly and easily attached to the stick of an excavator. Attachment to a leader or fitting in the clamp of a vibrator are available as options.
Applications
- Pre-drilling to loosen and relieve the ground
- Heavy soils
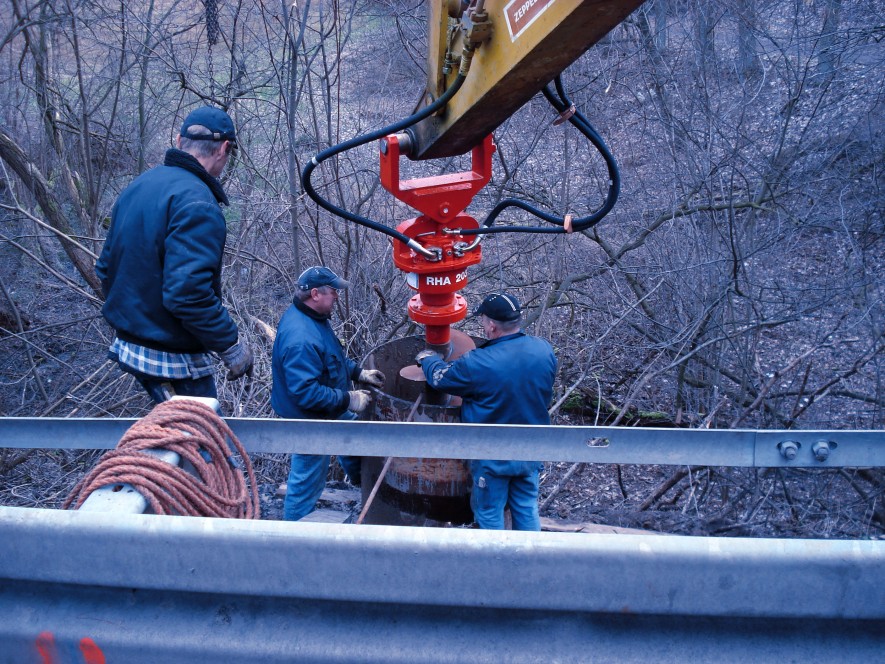
Power packs. Power and intelligence.
Power packs are needed to supply the hydraulic vibrators with energy. Inside a noise-insulated housing, diesel motors run hydraulic pumps that supply the necessary flow rate for hydraulic motors via hoses to the vibrators.
The low-noise, fuel-efficient integrated diesel motors comply with the latest exhaust emission regulations. The programmable logic controller can be operated via cable or radio remote control and is used to optimize and monitor the workflows. Optionally, operating parameters and machine data can be called up remotely online via data modem.
Advantages
Compact, lightweight design thanks to closed oil circuit High degree of reliability through the use of components such as diesel motors, pumps, and controllers that have been tried and tested on the building site Extensive range of accessories, such as a remote maintenance package, winter package, or fine bypass filters
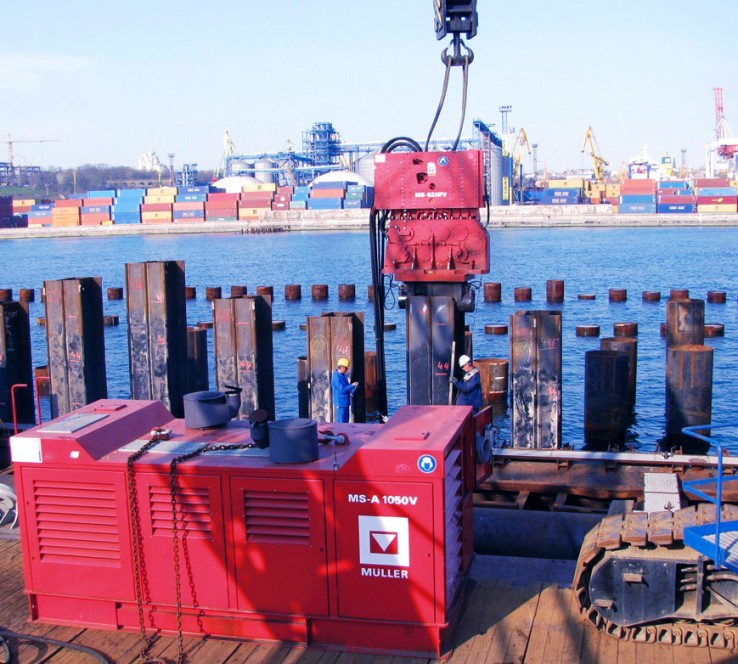
A safe connection: müller clamping devices
müller clamping devices
Clamping devices connect the pile section, e.g., pile sections, posts, H-beams, or tubular piles, to the vibrator and transfer the vibrations. The clamping devices can be rotated through 90° for face working. Adapter plates are available to cope with different clamping arrangements.
Clamps to fit over the interlocks of double piles and radial clamps for driving tubular piles are also available. Important for making the right choice: the clamping force of the device must be at least 1.2 times the centrifugal force of the vibrator. Can be used as single and double clamps for U/Z-sections, H-beams, and tubular piles, and as special clamping devices for specific tasks, such as for timber piles, concrete piles, and small-diameter tubular piles.
Applications
- As single and double clamps for U/Z sections, H sections, and tubular piles
- As special clamping devices for specific tasks, e. g., timber piles, concrete piles, and small-diameter tubular piles
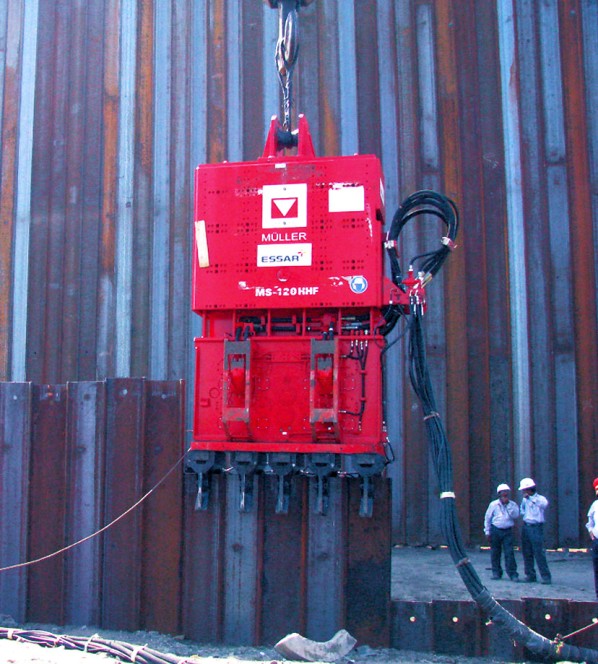
Special equipment. Special expertise.
Compactor plate
Compactor plate for compacting surfaces. Can be clamped quickly and easily into the clamping unit of a müller excavator-mounted vibrator.
Adapter plates
Adapter plates and double clamping units for clamping small pipe diameters with müller excavator-mounted vibrators.
Special construction
Special construction for driving pipes with a large diameter and weight.
Data collection
For controlled placement of the piling element when working in vibration-sensitive areas. Collecting, recording, analysing and storing of pile-driving data.
Simulation
Simulation of static and dynamic loads on new and extension rail tracks.
Equipment selection guide – Which piece of equipment for which requirements?
Choosing the right machine is crucial for the economic and technical success of vibratory driving. In order to find the most suitable equipment, we offer our customers individual support that takes into account all relevant factors, i.e., the site conditions plus the geological and engineering requirements.
Parameters
Selecting a suitable vibrator essentially depends on the size and weight of the pile section, the embedment depth, and the type of soil. Basically, the centrifugal force and the amplitude must be chosen in such a way that the skin friction and tip resistance between the pile section and the surrounding soil can be overcome.